Carbon fibre: Properties and End Uses
Last updated on August 10th, 2023 at 07:57 pm
Introduction
In 1963 a team of British scientists, W. Watt, W. Johnson, and L.N. Phillips, working at the Royal Aircraft Establishment, Farnborough, U.K., developed techniques for producing carbon fibres of high strength and outstanding rigidity. These fibres were in commercial production by 1968 and have since become of great importance, especially in the field of composites in which the fibres are embedded in resins or other materials.
Most of the important textile fibres in use today are derived from organic polymers, i.e., polymers in which the backbone of the molecular structure consists of carbon atoms to which are attached atoms of other elements, commonly hydrogen, oxygen, and nitrogen.
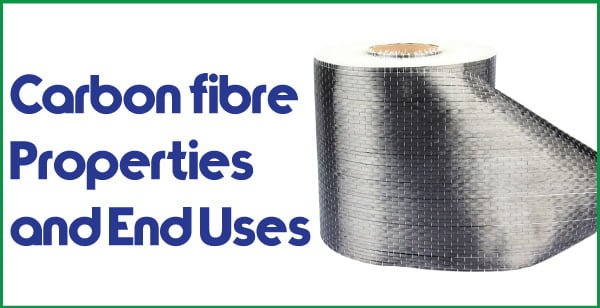
It has long been known that pyrolysis of these fibres, such as rayon, could result in the removal of the non-carbon atoms to leave a filament consisting essentially of carbon. But the carbon atoms in these filaments are arranged in more or less disordered forms; the structure is amorphous rather than crystalline, and the filaments are weak and of little practical value. To achieve high strength and modulus, it was necessary to devise a process for producing carbon fibres that would orientate the carbon atoms and result in fibres of a high degree of crystallinity.
Production Process of Carbon Fibre
The starting material for the production of carbon fibre is commonly an acrylic fibre, such as ‘Courtelle’, in which the backbone of carbon atoms is attached to a hydrogen atom and CN groups. A three-stage heating process is used in converting acrylic fibre to carbon.
The initial stage is to heat the acrylic fibres at 200-3000 C under oxidizing conditions. This is followed by a second stage when the oxidized fibre is heated in an inert atmosphere to temperatures around 10000 C. Hydrogen and nitrogen atoms are expelled, leaving the carbon atoms in the form of hexagonal rings which are arranged in oriented fibrils.
Finally, the carbonized filaments are heated to temperatures of up to 30000 C, again in an inert atmosphere. This increases the orderly arrangement of the carbon atoms which are organized into a crystalline structure similar to that of graphite. The atoms are in layers or planes which lie virtually parallel to each other. The planes are well oriented in the direction of the fibre axis, this being an important factor in producing high modulus fibres.
The mechanical properties of carbon fibres produced in this way are affected greatly by the conditions under which they are treated in the final stage, and by varying these conditions it is possible to produce fibres of different modulus and strength characteristics.
Structure and Properties of Carbon Fibre
The properties of carbon fibres vary, depending on the conditions under which they are produced. The information which follows relates to a typical range of fibres.
- Fine structure and appearance – Carbon fibres are black and smooth-surfaced, with a silky lusture. They are common of round cross-section, possibly with flattened sides.
- Ultimate tensile strength – 1.80 to 2.40 KN/mm2. (cf. steel 2.80-4.00).
- Breaking Extension – 0.5%. (cf. steel 2.0%).
- Density – 1.95 g/cm3. (cf. steel 7.80).
- Stiffness – 350-410 KN/mm3 (cf. steel 207).
- Stiffness/Weight Ratio – 180-210 (cf. steel 27).
- Elastic properties – load/extension curve almost linear to break. Hooklean behavior. Perfectly elastic to break.
- Specific gravity – 1.75-1.85
- Effect of moisture – Nil
- Flammability – Not flammable
- Effect of Age, sunlight – Nil
- Effect of chemicals, solvents – Inert. Hot air oxidation and strong oxidizing agents (e.g. sodium hypochlorite) cause some erosion.
- Effect of insects and Microorganism – Nil.
Carbon fibre in Use
Carbon fires are characterized by high strength and great stiffness against bending and twisting forces. Steel fibres, which approach nearest to carbon in stiffness, are four times as dense as carbon, and carbon fibres have a very much superior stiffness to weight ratio.

The breaking extension of carbon fibres is low, and unsupported fibres are brittle. Applications lie very largely in the field of composites for specialized uses, where the high cost of carbon fibre relative to steel, fiberglass, and other reinforcing fibres is of minimal consequence. Carbon fibre composites are used, for example, in aircraft structural components, in brakes and engines. They have proved of immense value in space vehicles, where weight reduction is at a premium. As carbon fibres become cheaper with increased production, they are finding their way steadily into more mundane applications such as golf-club shafts, fishing rods, boats and submarines, pressure vessels in the chemical and allied industries.
Special grades of carbon fibre are used in protective clothing fabrics, where their inertness and heat resistance serve them well. Carbon fibre fabrics may be washed at 400C and dried with a short spin tumble dry or calendar. They may be ironed and dry cleaned.
You may also like: Properties of Jute fibre
NICE ARTICLE..THANKS…
Do you have a spam issue on this website; I also am a blogger, and I wanted to know your situation; many of us have developed some nice methods, and we are looking to trade methods with others, why not shoot me an e-mail if interested.