Block Printing Method: An Overview
Last updated on August 3rd, 2023 at 10:53 am
Similarly to the art of screen printing, block printing originated in the Far East. India and China are the probable birthplace of block printing as, according to historians, their people used hand carved wood blocks for the production of ornaments on textiles. The principle of this method remains the same; the blocks are made by more modern methods.
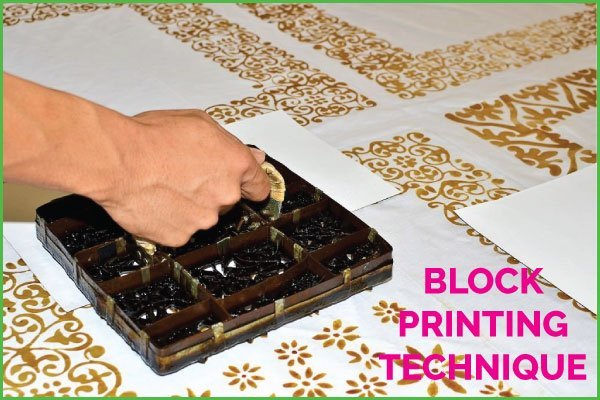
The blocks are generally about 3 inches thick and are preferably made of sturdy plywood. When design is to be carved by hand, a hardwood surface is used. Suppose when a 40 inch cloth is to be printed, the weight of the block would be too great to provide only a lengthwise repeats; the block therefore, is made smaller and carries side repeats of the pattern as well. In the preparation of blocks, therefore, not only the continuity of the pattern is taken into consideration, but also the width of the cloth, which determines the size of the blocks.
Formerly, after tracing the pattern on the surface of the block, it was carved out by hand. Now, this technique is partly replaced by use of a metal plate, on which the design appears in relief. For teaching the art of block printing some textile and art schools use a wooden block, to which a heavy piece of linoleum is attached. The students then carve the desired design into the linoleum layer.
The table on which block printing is done is similar to a screen printing table, but its surface is preferably harder.
The supply of print paste is carried on a specially constructed table on wheels. The print paste, which is kept considerably thinner (or softer) than for screen printing is in a container covered with thick felt. This felt is saturated with the paste and from the felt the color is transferred to the block surface by laying the block on the felt. The block, when picked up, must show an even coverage of color paste on the surface, this is then transferred to the cloth to be printed.
The preparation of print paste and all methods of finishing are the same as for machine printing.
Block printing, representing purely manual productions is used very little, if at all, for commercial purpose. It has been practically completely replaced by the much more efficient screen printing.
Design is engraved on wooden, linoleum or copper blocks; dye is applied to the raised areas of the designed blocks, block is pressed on the fabric, desired color and design is transferred to base fabric. Procedure is repeated design as many times as design is desired. Multicolored patterns require separate blocks for each color.
You may also like: Top 5 Batik Printing Methods