What is Fusible Interlining | Construction of Fusible Interlining
Last updated on September 19th, 2023 at 11:50 am
Introduction
Every clothing manufacturer continually attempts to produce garments with immediate sales appeal. However, one of the most important materials used for nearly every item of outerwear has no sales appeal because it is invisible to the consumer. This material is the fusible interlining. Since it was first introduced in the early 1950s, it has become an integral component of garment construction.

Definition
The term fusible interlining is used to describe a base fabric coated on one side with a thermoplastic adhesive resin that can be bonded to another fabric by the controlled application of heat and pressure. These materials, generally called fusible, provide the designer with several properties that can enhance the appearance of finished garments by the following:
- Control and stabilization of critical areas.
- Reinforcement of specific design features.
- Minimum of modification to the ‘handle’ of the top cloth.
- Preservation of a crisp and fresh look.
Correctly selected and applied, fusible has many advantages for the designer, the production unit, and the consumer.
Construction
A fusible combines the following three factors in its construction:
Base material – Also called the substrate.
Thermoplastic resins – Synthetic resins melt when subjected to heat and revert to their original solid state when cooled.
Coating – The amount of resin deposited and how it is secured onto the base fabric.
The following figure shows the basic construction of a fusible and illustrates how the resin is disbursed into the top cloth when the two layers are bonded. The finished bond is referred to as a laminate.
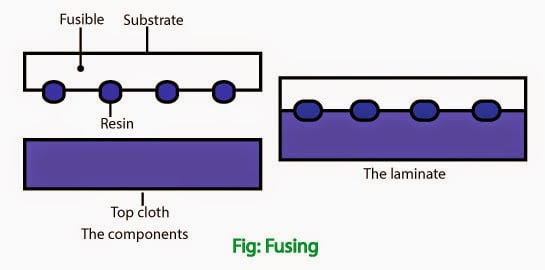
Base Materials
The base materials are produced in a diversity of woven, knitted, and nonwoven forms, with each type having its particular application according to its intended function on the garment. The materials can be produced from natural or synthetic fibres or blends of each of these fibres. Base cloths influence the following characteristics of the finished garment:
- Handle and bulk.
- Shape retention.
- Shrinkage control.
- Crease recovery.
- Appearance after washing or dry cleaning.
- Durability.
The properties of different base materials sometimes overlap to a considerable extent so the following descriptions some general insertions.
Resins
Resins are the sole bonding agent between the top cloth and substrate and irrespective of the type of resin used; they have to conform the following conditions:
Upper-limit temperature – The resin should become viscous at a temperature below that which would damage the top cloth. Whilst this temperature varies according to the consumption of the top cloth, it rarely exceeds 1750 C.
Lower-limit temperature – This is the lowest temperature at which the resin starts to become viscous. For most fusible this is about 1100 C, and for the fusible used for leather and suede materials, the temperature is considerably lower.
Clean ability – The adhesive properties of the resin have to be sufficiently strong to withstand washing or dry cleaning throughout the normal life of the garment.
Handle – The resin must contribute to the required handle and nonact as an unwanted stiffening agent on the final laminate.
Resin Types and Applications
The type and properties of the most widely used resins are –
Polyethylene – At different densities, this is suitable for wash and wears garments or for those which have to be dry-cleaned only.
Polyamide – All polyamide resins produce full dry-cleanable and washable bonds but there is a class of this resin that is dry-cleanable only.
Polyester – These resins have the same general properties as polyamides but are generally a little cheaper.
PVC – Used extensively for siliconized rainwear fabrics.
Plasticized polyvinyl acetate – A multi-purpose resin that is both washable and dry-cleanable.
Plasticized polyvinyl acetate – Mainly used for leather, but it is not dry-cleanable and has very limited washability.
Coating
There are two aspects of the coating – density and coating system.
Density
Resins are applied to substrates in three different densities – low, medium, and high – and the degree of density refers to the actual mass per unit volume of the resin material. This physical density is directly related to the melting point of the resin and its resistance to dry-cleaning solvents. As a rule, the higher the density, the better the resin stands up to dry cleaning.
Coating System
This refers to the process whereby the resin is deposited and secured on the substrate. There are three principal methods:
Scatter coating – This method uses electronically controlled scattering heads to deposit the resin crystals on to the moving substrate surface is covered with resin, which reduces the flexibility of the laminate.
Dry – In this process, the resin is printed onto the substrate in regularly spaced dots using rollers with indentations that hold the resin crystals. This method is generally regarded as producing the most flexible bond.
Preformed – The resin is heat processed to form a net which is then bonded onto the substrate by heat and pressure. During heating, the net melt’s link lines leave a minute dot pattern on the base cloth. This method is also used to produce paper-backed tapes, which are used for fastening hems and facings instead of blind stitching or felling.
You may also like: What is Interlining? Types of Interlining