Sectional Warping Machine
Last updated on October 18th, 2023 at 12:22 pm
Woven fabric is produced by the weaving process in the weaving mills. Sectional warping is an important process in these weaving mills. It is used to produce warp beams for weaving. So it is the preliminary process of weaving. In this article, we will learn about the sectional warping machine working process.
Introduction
The sectional warping machine prepares multicolored warps to be woven as striped or checked design fabrics. It is additionally used for doubled grey or mono-colored warps that do not require sizing. Unlike the beam or direct warping, where a warper’s beam is manufactured and sent to the consequent sizing processes, in the case of sectional warping, the weaver’s beam is manufactured and hence does not require sizing. In the case of single yarns that are multicolored, the yarns are sized and then coiled on the sectional warp beam. The yarn is wound in sections, each section having a particular width. Thus the total number of warp ends for the weaver’s beam is arranged into a suitable number of sections on a warping drum. The sections are then consolidated to form the weaver’s beam. Therefore, there are two separate operations involved, namely, warping and beaming.
Passage of Yarn Through the Machine
The passage of material through the sectional warping the machine is shown in the following figure:
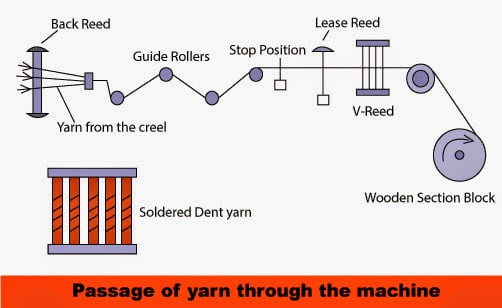
The supply packages are in the form of cones or cheeses. They are placed on a V-shaped creel or a semi-circular creel depending upon whether stop motion is used or not.
The yarn from the creel moves through the back reed. The reed controls the uniform spacing of the yarn throughout the width of the warp.
Then the yarn moves over and under the guide and drop rollers. The drop rollers impart tension to the yarn passing under them and hold the yarn tight when the machine is paused.
From there, the yarn goes through a stop motion device which stops the machine in the event of an end breakage in the supply package, getting exhausted.
From the stop motion device, the yarn moves through a leasing reed. The reed is to form an end and end lease at the start and completion of each section. The depth of the reed is comparatively much more than that of the common reed. Each end of the warp passes separately inserted in the warp after one section of warp, and the reed is lowered.
You may also like: What is Beam Warping | What is Creel | Types of Creel
This will bring all the alternate ends moving through the soldered dents, i.e., alternate ends passing through the soldered dents down, i.e., alternate ends will from the bottom line and another set form a top line. The division of warp threads is named shed. Now a lease band is inserted. As soon as it is finished, the reed is lifted. This will cause an alternate set of warps, which were down in the previous operation, to be lifted and those on the top to be lowered. Now another lease band is inserted, and the reed is brought back to its normal position, i.e., middle position.
The purpose of this leasing is to wind and unwind the warp without any entanglement between threads to distribute evenly. It also helps the yarn maintain in position and helps to detect the broken end and mend it properly.
The yarn next passes through a V-reed, enabling the warp’s width through it to be adjusted according to the width of the sections to be made.
Then the yarn passes over a measuring roller and is wound on a wooden block called swift. After winding the predetermined length of warp, leasing is carried out. The sections of threads are continued to the swift in a bunch form. Next, the section is wound in the side of the previous one. The exact process is continued until the required numbers of sections are made on the wooden swift. Then all the sections are taken and transferred to a beam using the running-off machine. The beam is driven by a motor or manually. The section width may vary from 10 cm to 20 cm.
Merits and Demerits
The sectional warping machine has the following advantages:
- It is suitable for striped warp yarn.
- The labor charge is not so high.
- Low power is required to drive the machine.
- There is no sizing process.
The demerits are:
- There are two stages, namely, warping and beaming.
- Warp will have to be dyed, sized, and dried separately by slow and expensive processes before warping.
- Some amount of size will be removed from the warp during the process of sectional warping.
very good post, i surely enjoy this fabulous website, continue it