Raw Materials Used in Textile Industries
Last updated on June 24th, 2023 at 05:32 am
Raw material (RM) is the primary substance which is used as an input to a production process for subsequent modification and finally modified into a finished good. Raw materials may be in processed or unprocessed state. Most of the times raw materials are natural resources such as cotton, oil, rubber etc. They are also altered to be used in different processes before being used in the final manufacturing process. So we can say that, the processed or unprocessed materials which are used to produce final textile products are called TRM.
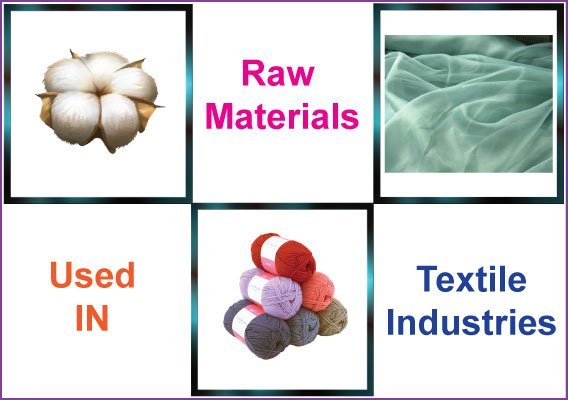
Types of Textile Raw Material
TRM may be of different types as follows –
- Fibre
- Yarn
- Fabric
- Dyes
- Chemicals and Auxiliaries
Fibre
The textile industries use different types of fibres which are derived from nature or manually produced. These fibres are used to produce dresses, towels, blankets etc. Some of these fibres were known and used in the earlier years of civilization, as well as in modern times. Other fibres have acquired varied degrees of importance in recent years. The factors influencing the development and utilization of all these fibres include their ability to be spun, their availability in sufficient quantity, the cost or economy of production, and the desirability of their properties to consumers.

Classification of Textile Fibre
Type | Name of Fibre | Source or Composition |
---|---|---|
Vegetable | 1. Cotton 2. Linen 3. Jute 4. Hemp 5. Sisal 6. Kapok 7. Ramie 8. Coir 9. Pina | 1. Cotton ball (Cellulose) 2. Flax stalk (Cellulose) 3. Jute stalk (Cellulose) 4. Hemp or abaca stalk (Cellulose) 5. Agave leaf (Cellulose) 6. Kapok tree (Cellulose) 7. China grass (Cellulose) 8. Coconut husk (Cellulose) 9. Pineapple leaf (Cellulose) |
Animal | 1. Wool 2. Silk 3. Hair | 1. Sheep (Protein) 2. Silkworms (Protein) 3. Hair bearing animals (Protein) |
Mineral | Asbestos | Varieties of rocks (silicate of magnesium and calcium) |
Cellulosic | 1. Rayon 2. Acetate 3. Triacetate | 1. Cotton linters or wood 2. Cotton linters or wood 3. Cotton linters or wood |
Noncellulosic Polymers | 1. Nylon 2. Aramid 3. Polyester 4. Acrylic 5. Modacrylic 6. Spandex 7. Olefin 8. Vinyon 9. Saran 10. Novoloid 11. Polycarbonate 12. Polybenzimidazole 13. Alginate 14. Fluorocarbon 15. Graft 16. Matrix 17. Anidex 18. Lastrile 19. Nytril 20. Vinal | 1. Aliphatic polyamide 2. Aromatic polyamide 3. Dihydric alcohol and terephthallic acid 4. Acrylonitrile (at least 85%) 5. Acrylonitrile (35% – 84%) 6. Polyurethane (at least 85%) 7. Ethylene or propylene (at least 85%) 8. Vinyl chloride (at least 85%) 9. Vinylidene chloride (at least 80%) 10. Phenol based novalac 11. Carbonic acid (polyester derivative) 12. Tetraminobiphenyl & diphenyl isophthalate 13. Calcium alginate 14. Tetrafluoroethylene 15. Molecular graft of polymers 16. Mixture of polymers 17. Monohydric alcohol & acrylic acid 18. Acrylonitrile (10-50%) and a diene 19. Vinlylidene dinitrile (at least 85%) 20. Vinyl alcohol (at least 50%) |
Protein | Azlon | Corn, Soybean |
Rubber | Rubber | Natural or Synthetic rubber |
Metallic | Metal | Aluminum, silver, gold, stainless steel |
Metal | 1. Glass 2. Ceramic | 1. Silica sand, limestone 2. Alumina, silica |
Yarn
Yarns can be made of staple fibres by several techniques. The method used is dependent upon such factors as the economic implications, the fibres to be used and desired properties of the yarn to be produced. Rings pinning is the oldest and most wide spread technique. Open end spinning is another major method. The development of short fibres, or staple, into yarn, when started in terms of basic manufacturing processes, is as follows:
Carding
↓
Combing
↓
Drafting
↓
Twisting
↓
Winding
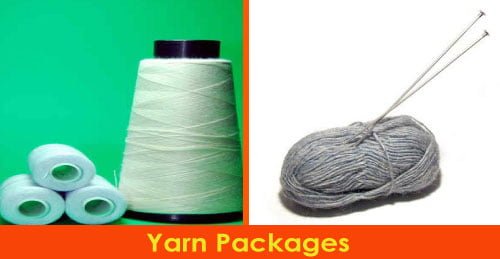
As the fibres pass through these processes, they are successively formed into lap, sliver, roving and finally yarn. Here the manufacturing operation in which these stages occur:
- Lap to card sliver by the carding process
- Card sliver to comb sliver by the combing process (if the fibre is to be combed)
- Sliver to roving by the drafting, or drawing process
- Yarn reeled on bobbins, spools or cones by the winding process
Fabric
Fabric is a planar textile structure produces by interlacing yarns or filaments. Most fabrics are produced through knitting or weaving, but some are produced by non-woven processes such as braiding, felting, and twisting.
Weaving
A major method of fabric construction is weaving. The technique probably became known before spinning. Primitive people may have observed the interlaced grasses and twigs in the nests of birds, and thus discovered how they could make clothing for themselves. Spinning developed when people discovered that the raw materials could be improved before they were woven. In course of time, rude looms were made, which were crudely simple and hand-operated. The modern power loom used in the textile industry today essentially performs the same operations as the simple hand operated loom.
Knitting
Knitting is the second most frequently used method of fabric construction. The popularity of knitting has grown tremendously within recent years because of the increased versatility of techniques, the adaptability of the many new man-made fibres, and the growth in consumer demand for wrinkle resistant, stretchable, snug-fitting fabrics, particularly in the greatly expanding areas of sportswear and other casual wearing apparel. Today, the usage of knitted fabrics ranges from hosiery, underwear, sweaters, slacks, suits and coats, to rugs and other home furnishings.
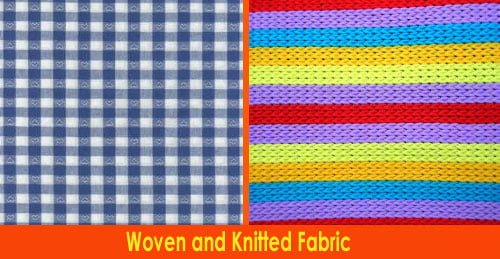
Some commercial names of fabric are as follows:
- Aertex
- Angora
- Braid
- Brocade
- Chiffon
- Canvas
- Chambray
- Denim
- Fleece
- Hopsack
Dyes
The dye is a complex compound which is applied in the textile materials represent color and contains chromophore and auxochrome groups in its chemical structure. It is necessary to know which dyes have an affinity for the vegetable, animal, or man-made fibres to select the proper dye for a fibre.
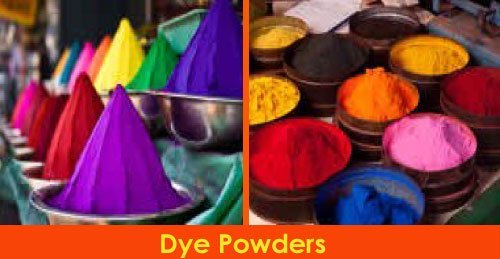
Different types of dyes are used in the textile industries as raw materials are as follows –
- Basic dyes
- Acid dyes
- Mordant dyes
- Substantive direct dyes
- Developed dyes
- Azoic dyes
- Disperse dyes
- Vat dyes
- Reactive dyes
- Pigment dyes
Chemicals and Auxiliaries
Dyeing chemicals and auxiliaries enables a processing operation in preparation, dyeing, printing or finishing to be carried out more effectively, or which is essential if a given effect is to be obtained.

Different types of chemicals and auxiliaries used in dyeing, printing and finishing are as follows –
- Whitening agent
- Wetting agent
- Fixing agent
- Detergent
- Silicon
- Water proofing agent
- De-foaming agent
- Enzymes
- Caustic soda
- Soda ash
- Acetic acid
- Oxalic acid
NICE INFORMATION.THANKS.
Mtek Sourcing is also the leading metal casting sourcing company in India that exports its metal casting components to Australia, UK, USA, Canada, & other European countries.
COLDMAN is into providing Temperature-Controlled Warehousing & Logistics Services to various Industries with a strong focus on technology driven operations .We offer End to End Solutions from Source to Consumption point.
I’m consistently impressed by the depth of your knowledge.