An Overview of Fusing Process
Last updated on September 11th, 2023 at 09:47 pm
Fusing Process
Regardless of which fusible and machine are used, fusing is controlled by four processing components – temperature, time, pressure and cooling and these have to be accurately combined in order to achieve the optimum results.
Temperature
There is a limited range of temperatures that are effective for each type of resin. Too high temperature causes the resin to become too viscous, which could result in the resin being forced through the right side of the cloth. If the temperature is too low, the resin is not sufficiently viscous to disburse into the top cloth. In general, resin-melt temperatures range from 1300 to 1600 C and the best results will normally occur within ± 70C of the temperature specified by the manufacturer of the fusible.
Time
The only time element of any value during the fusing process is when the top cloth and fusible are under pressure in the heating zone of the machine. This time cycle for a particular fusible is determined by:
- Whether the fusible has a high or low melt resin.
- If a light or heavy substrate is being used.
- The nature of the top cloth being used, i.e. thick or thin, dense or open.
Manufacturers of fusible supply data sheets which give the time cycle for each fusible, and this refers to the actual fusing stage only.
Pressure
When the resin is viscous, pressure is applied to the top cloth and fusible assembly to ensure that:
- Full contact is made between the top cloths and fusible.
- Heat transfer is at the optimum level.
- There is an even penetration of the viscous resin into the fibres of the top cloth.
Most fusing machines use two steel rollers or pressure plates to create pressure, but a flexible pressure system has been developed which automatically adapts itself to variations in the thickness of the assembly being fused, whilst maintaining an even pressure over the entirely assembly.
Cooling
Enforced cooling is used so that the fused assemblies can be handled immediately after fusing. Cooling can be induced by various systems, including water-cooled plates, compressed air circulation and vacuum. Rapidly cooling the fused assemblies to 300 to – 350 C makes for a higher level of productivity than if operators have to wait for the assemblies to cool naturally.
The fusing process produces what is, in effect, the foundation of a garment and the best results can only be achieved when there is an accurate and continual control of the four processing components.
Fusing Machinery
A press is used for fusing and three basic types are:
- Steam press
- Flat bed press
- Conveyor belt press
Each type of machine has its own range of capabilities.
Steam Press
Regular steam pressing machines are not designed for fusing although some fusible are produced for use on these machines. Pressing machines have some serious limitations regarding fusing including:
- Inability to reach the heat levels required by the majority of resins.
- The shape and size of the bucks restrict the size of the components which can be fused.
- Most utility machines are not fitted with programmed controls, which mean that the entire process is operator controlled.
- If the resin was originally activated by steam heat, the same thing can happen when garments are pressed during their production. This situation can cause serious problems with the stability of the laminates.
Regular steam pressing machines are not the ideal medium for fusing.
Flat Bed Press
Flat bed presses are purpose built fusing machines produced in a large variety of sizes and which many types of work aids. This type of press has padded top and bottom bucks with electric heating elements in one or both bucks. The bottom buck is static and the top buck is lowered to fuse the assembly whilst under pressure, and then raised after cooling. Most of these machines are fitted with timers and programmed controls and can achieve high levels of fusing quality.
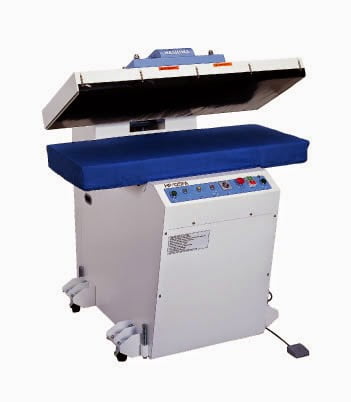
Conveyor Belt Press
Conveyor belt presses are also called continuous machines because they can be operated without stopping for the loading and unloading of the assemblies. The conveyor belt transports the assemblies through all the processes and the belt speed is adjustable according to the time cycle required. This type of machine is available in different lengths and widths and can be fitted with automatic feeding and unloading systems. A feature of the more modern machines is a microprocessor which can be programmed to control every element of the machines operation.
pls send me a quotation for above machine.
May I request that you elaborate on that? Your posts have been extremely helpful to me. Thank you!