Transfer Printing Method
Last updated on August 4th, 2023 at 08:24 pm
The ability of disperse dyes to sublime on heating has led to a very different approach to textile printing. In this the design is first printed on paper using disperse dyes. The paper can then be inspected for faults; if any exist, that area of paper can be discarded to avoid wastage of fabric. The fabric is placed face down on the printed surface of the transfer paper, and the two are squeezed together in a heated press at a temperature high enough to vaporize the dye, which transfers in the vapor phase to the fabric. Transfer printing has the advantage that no printing paste is applied to the fabric and so no washing-off is necessary.
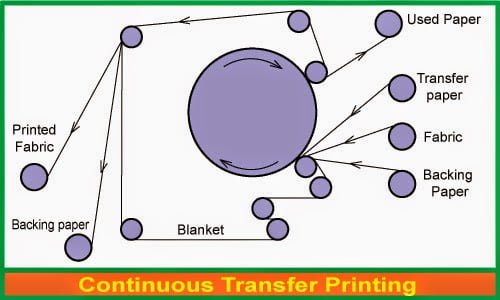
The production of transfer printing paper for textile purposes began to grow rapidly in the early 1970s but so far its use is restricted to the application of disperse dyes, and hence to the printing of synthetic fibres. The paper can be prepared by gravure printing, in a manner similar to the engraved roller printing of textiles. An alternative is flexographic printing, in which the image is formed in relief on a composite rubber molding using sophisticated methods for cutting the pattern; this method has the advantage that wide paper may be printed satisfactorily. Another method is lithographic printing, which involves the preparation of a discontinuous design on a plate by photographic techniques.
The fabric and paper are brought into close contact using a continuous calender type of processor (above figure). The fabric and paper are placed face to face and held close to a heated cylinder under light pressure from an endless blanket, often made of the heat-resistant material Nomex. Fast rates of production are possible with this system.
tnx