Faults found in Speed/Simplex/Roving frame with Causes and Remedies
Last updated on October 18th, 2023 at 06:06 pm
Simplex Machine is used in the spinning mills. For Ring yarn Simplex machine is necessary. Simplex machine is the machine which converts the drawn sliver into roving form. Simplex process is the previous process of ring spinning process. A slight twist is given onto the roving.
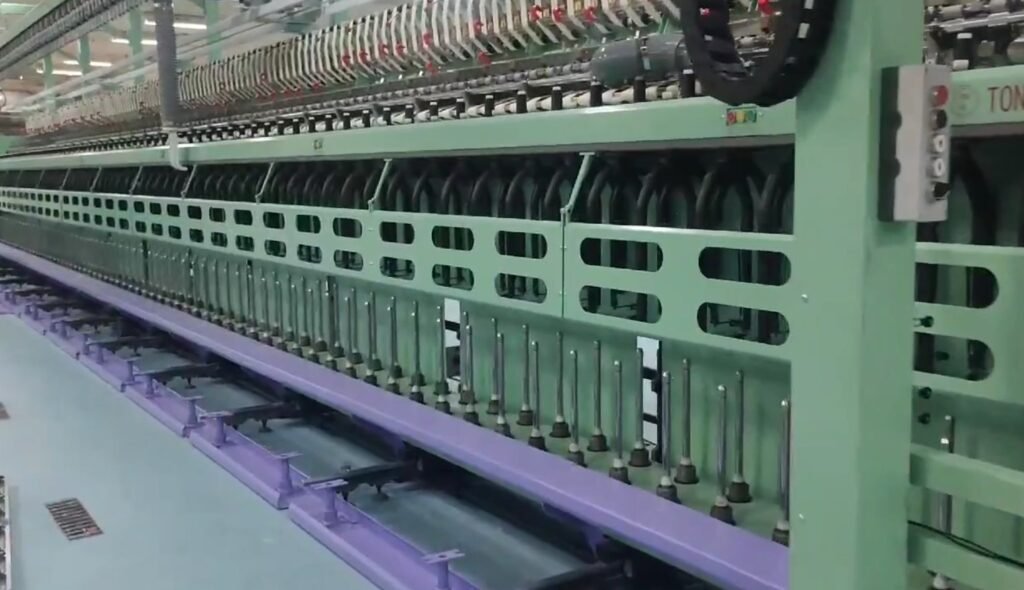
We can find different faults in the speed/roving/simplex frame. They are described below –
Ratching
It is defined as undesired stretching of the roving to make it finer and it produces a high count variation.
Causes: Larger lifter wheel, or winding wheel, or ratchet wheel, or starting with half layer.
Remedies: This defect can be cured by using a correct smaller lifter wheel, winding wheel and ratchet wheel or rack wheel. At the start of a new doff the bobbin rail should be taken up or down to start with a full layer instead of a half layer which will produce uneven tension during winding the next layer on the bare bobbin.
Unequal tappers
This defect will occur if the pocker rack is not perfectly level when the pressure eye is at the middle of the lift. To equalize the tappers, mark the exact centre of the barrel portion of a bobbin and place the bobbin and a flyer in their working position. Mark the top rail until this is in the centre of the pressure eye and then level the two bars and the rack pocker by spiraled level. Reset the adjusting screws in the pocker bracket so that they operate the motion catches correctly at the top and bottom of the lift.
Stretched roving
Stretching is due to the difference in surface speed between the bobbin and the pressure eye being greater than the surface speed of the front roller. It occurs throughout the build, reduces the bobbin speed by using a smaller bottom cone drum change wheel.
If stretching gets progressively worse in the bobbin build up, building motion ratchet wheel to be with fewer number of teeth or the spur wheel change building motion to be adjusted to give the same effect. This will make the cone drum belt along the cone drums at a higher rate and thus gives a greater reduction in bobbin speed as the package diameter increases.
Too small a lifter change wheel can cause this defect through adjusting coils tending to ride on one another. This wheel is to be made larger.
An accumulation of waste in the legs of the flyers will lead to stretching the individual spindles. In this case the roving will be slack between the front rollers and the affected flyers.
Sloughing
Causes:
- Sloughing at the bobbin ends may be due to reversing bevels which are badly worn or too shallowly meshed.
- Motion catches with worn ends.
- Insufficient taper on the bobbins.
- Balance weights not fitted correctly or touching the floor.
- Hesitation at the change over either the building motion or the reversing mechanism resulting from dirt, tightness or incorrect setting.
Remedies:
- The worn bevels should be replaced.
- Correct shape of the motion catches.
- Correct tapper of bobbins.
- Proper setting of the related parts.
Incorrect tapper
This defect can be rectified by changing the tapper wheel. Reduce number of teeth in the tapper wheel reduces the tapper and vice-versa.
Ridgy bobbins
Faulty movement of the top rail results in ridgy bobbins at the bobbin ends.
Causes:
- Tight or badly worn lifter shaft bearings.
- Dirt on the top rail sides.
- Worn revering bevels.
- Slack lifter shaft pinions.
- If the balance weight touch the floor when the rail is at the top of its lift.
- Foul the chain pulleys at the bottom of the lift.
Remedies:
- Faulty bearing should be removed.
- The top rail should be cleaned.
- Worn bevel should be removed.
- Lift shaft pinion should be properly secured.
- Correct setting of the balance weight.
Soft bobbin
Causes:
- Too quick reducing of the bobbin speed as the package builds up in bobbin leading frame.
- Too high speed of top rail, giving excessive spacing of the coils.
- Individual soft bobbin may be due to: Incorrect threading of the roving round the flyer tap. Insufficient number of turn of the roving round the pressure arm. Lifting bobbin wheel. Removal of the long length of thick or single roving.
Remedies:
- Large ratchet wheel or same effect with spur wheel change building motion.
- A smaller top lifter change wheel.
- Correct threading adjustment and piecing up.
Single and double
Single may be due to –
- Slubs in the material being fed may prevent in passing through the back guide and results in the formation of single.
- By piecing the full bobbins to the wrong end when creeling.
- By lapping due to rough places or oil on the roller.
Doubles may be due to –
- Broken end at the front lasting into an adjustment end and being carried forward with it.
- Long piecing with creeling.
Any single or double in the previous process may also cause this effect.
Remedies:
Care must be taken for the above reasons of single and double so that they might not occur.
Cut roving
Causes:
- Too close setting between two lines of drafting rollers.
- A strained bottom roller.
- Broken teeth in the draft gearing.
- Roller gearing set too deeply in mesh.
- Badly worn cap bar slides.
- Loose sections of bottom rollers.
- Badly pieced roller coverings.
Remedies:
We should maintain the proper settings of the machine parts.
Slubs
Causes:
- Waste from the creel or clearers passing forward with the materials.
- Loose fly accumulating on top of the creel bobbins and being incorporated into the roving.
- Waste gathered in the top and hollow legs of the flyers.
- Infrequent or insufficient cleaning of any port that comes into contact with the material being processed.
- A broken end at the front, lasting into an adjacent end, can also produce this defect.
Remedies:
Actions should be taken accordingly.
Snapping
Snapping is a severe form of stretching and usually means that the roving being subjected to excessive tension due to too high a bobbin speed in relation to the spindle speeds. The roving generally breaks at each pressure eyes.
Causes and remedies:
- If snapping occurs at an intermediate stage in the bobbin build, it will probably be caused by interference to the moment of the cone drum belt. This can be recognized by the fact that the lift is not being reduced. Check for the waste on the long rack and ensure that the long rack bowls revolve freely and that the rack pinion is firmly secured to the upright shaft.
- If snapping occurs at the end of the build, it indicates that the ratchet wheel is too large. Thus giving insufficient movement to the cone drum belt or that the gear train in the spur wheel type building motion is producing the same effect. This has a cumulative action, stretching progressively increasing as the bobbin build up until finally occurs.
- Too tight cone drum belt can produce this fault.
Dirt or oil strained roving
Causes:
- Excessive oiling of rollers, spindles or bobbin driving wheels may be the main cause of this fault.
- Cracked or broken bobbins, use of dirt boxes for transporting roving and oil on the top rail or clearer can also be lead to stained roving.
Remedies:
Correct oiling, cleaning etc.
Slack ends
Slack ends may always be caused by slack winding, a slipping cone drum belt, binding top rail slides, long collars clogged with waste and dirt, or too many turns of the roving round the pressure arm.
Incorrect twisting
Poor twist cause breakage prior to spinning and excess twist cause not to unwind during spinning in the break draft zone of the ring frame.
Excessive ends down
Causes:
- Cut drawing.
- Bobbin jumping.
- Broken teeth in head stock.
- Improper humidity.
- Loose coupling of spindle pinions on spindle shaft.
- Cone drums belt slipping.
- Traverse motion not properly set.
- Wrapping round bottom and top roller.
- Hollow, rough and worn out gearing.
- Slubs in roving.
- Cut roving.
- Improper pressure on the top roller.
- Waste accumulating in the pressure eye.
- Very badly keeping the under and top clearers.
Remedies:
Steps should be taken accordingly.
Irregular roving
Causes:
- Irregular sliver feed to the machine.
- Roller lapping.
- Groove in the top roller.
- Incorrect distribution of draft in the drafting zone.
- Tension draft.
- Incorrect weighting of the top roller.
- Incorrect roller setting.
- Single instead or double when used.
- Lack of proper maintenance, oiling, and cleaning.
tnx said bai
Good post. Thanks a lot.
You are most welcome
this post is helpful for us.Thank you brothers
Welcome bro.
Zinser 670 it says start-up not started