An Overview of Wool Scouring
Last updated on September 21st, 2023 at 12:12 am
Introduction
The term “scouring” in the generic sense of a process that that removes contaminates from raw wool. Thus, it includes all processes which aim to clean wool including those which use solvent other than water and those which use solid as a carrier for removing the contaminates.
Nature of Contaminates
The main contaminates of wool are wool grease, suint and dirt. Wool grease, technically a wax, is produced by the sebaceous glands in skin of sheep, while suint is produced by the sweat glands.
Typical concentration of non-wool contaminates (Percent by mass on greasy wool) are given below:
For Australian (New South Wales) Merino
Impurities | Maximum | Minimum | Average |
Grease | 25.4 | 10.0 | 16.01 |
Suint | 12.0 | 2.0 | 6.1 |
Dirt | 43.8 | 2.2 | 19.6 |
For New Zealand cross bread
Impurities | Maximum | Minimum | Average |
Grease | 8.5 | 1.6 | 5.2 |
Suint | 12.1 | 2.2 | 8.0 |
Dirt+suint moisture | – | – | 7.9 |
Historical Overview of Scouring Method
Traditionally, wool was scoured in hot, aqueous solution of soap and alkali. Synthetic detergent has replaced with soap but the main principle of aqueous solution still present. However, the use of volatile solvent to scouring wool in batch wise processes was introduced about 1900.
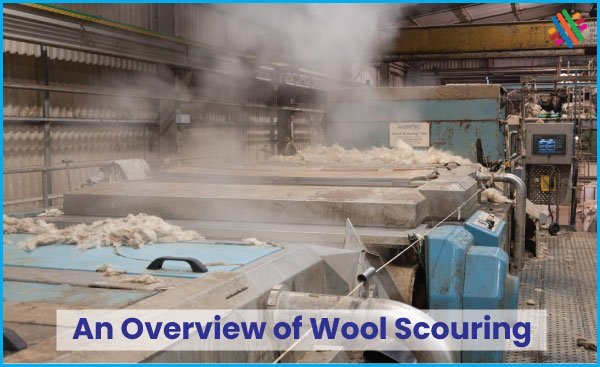
After that many development is done in scouring process. Many research organizations and laboratories have introduced many kind of technique and some techniques are in not use. Still many researches are going on and new technologies are coming forward.
Unit Operation
General overview
A wool scouring works typically includes facilities for blending and mechanically cleaning greasy wool and during and blending the scoured wool, as well as the scouring machine itself. The possibility of carrying out additional chemical processing may be provided.
Blending systems for greasy wool
Two basic types of blending systems may be identified.
- In-line blending system are used where the wool being blended have similar characteristics.
- Computerized weight belt blending systems are used for blending wools that have different characteristics.
Preheating bales of fine wool
Before densely packed fine wool is blended, preheating may be necessary to facilitate opening the wool. Fine wools are compressed to high densities to enable storage and lower the cost of transport. Preheating makes the compressed wool relaxed.
There three main methods of preheating. They are:
- Warm rooms
- Steam injection
- Microwave and dielectric heating method.
Opening and dusting
Wool may be opened and dusted after and before scouring.
Greasy wool is opened to remove contaminants in scour and assist the blending process. Opener-duster machines are used to avoid mixing the solid material in the liquor.
The scoured wool is opened to dry quickly and equal distribution of moisture.
Washing wool in the scouring train
A scouring train comprises many washbowls and squeezes the head, and is usually linked to an in-line dryer and a wool grease recovery system.
Older conventional scouring lines typically include four bowls having rake or harrow mechanism that dunk and transport the wool. This mechanism is so popular that this basic system is not changed. In the last several yare many techniques have been developed.
Squeeze head
The action of the squeeze roller is critical to the efficiency of removal of contaminants from the wool. As the wool mat enters the nip of the squeeze roller, it is subjected to intense hydrodynamic forces that are particularly efficient at removing wool grease, suint from wool fibre, and extra liquor scouring bath but less efficient for removing dirt.
Scouring Chemistry
Detergent and builders
Before the 1950s, soap was used to scour wool with an alkaline builder, usually soda ash. The property of soap is to form an insoluble salt with calcium and magnesium ion of hard water. To avoid the problem, detergent is used now these days. Non-ionic detergent is most popular in the scouring industries.
Soda ash (sodium carbonate) remains the most common builder used, although sodium chloride or sodium sulphate are sometimes used. The action of the builder is to stabilize the emulsified wool grease and dirt and prevent redeposition back on to the wool.
Water quality
There are two primary sources of problems associate with water quality: hardness and the presence of multivalent metal ions. While hardness, in the form of calcium and magnesium ions in the water, does not interface directly with the action of non-ionic detergents, their presence could cause redeposition of fibre contaminates and dying problem. It has been suggested that it is possible to scour greasy wool satisfactorily in water total hardness up to 70ng/litre, while unsatisfactorily scouring likely to occur on 100mg/litre. It may be necessary to install a softening plant in a hard water area to prevent such a problem.
Apart from calcium and magnesium, metal ions such as iron can cause severe dyeing problems by interacting with dyestuff.
You may also like: Cotton Vs Jute: Find the Key differences