Wool Production Process | Difference between Worsted and Woolen System
Last updated on October 18th, 2023 at 12:39 pm
Wool Production Process
Sheep are sheared to remove the fleece in the spring season. Wool removed from animals that have been slaughter is referred to as ‘pulled wool’. Pooled fibre is inferior in quality to fleece or tip wool as it is less lustrous and elastic. It can be spun into yarns by the woolen or the worsted system.
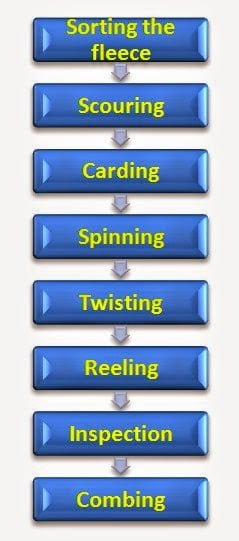
Sorting the fleece
Each wool fleece yields many diverse grades of these fibres. A skilled sorter can separate them by qualities called sorts.
The shoulder wool generally has the best fibre. Fine fibres that are comparatively long are reserved for sheer wool fabrics and worsteds. Medium fibres of the shortest length are suitable for woollens, while coarse fibres are suitable for carpets.
Scouring
It removes oils, grease, sweat and some of the dirt and impurities from the fleece. The fleece is washed several times in a warm, soapy alkaline solution. Scouring converts a fleece of 8 lbs to one of 3-4 lbs. The weight loss results from the removal of lanolin. This lanolin is recovered for use in cosmetics etc.
Carding
All the fibres are carded. Fine wire teeth mounted on a cylinder separate the fibres and make them somewhat, almost totally parallel. This procedure also removes remaining vegetable matter from the fibre. Yarns that have been carded are known as woolen yarns. Woolen yarns are carded only, and the fibres are rather random in arrangement. They still contain foreign matter which is removed by carbonization. i.e. treating with acid.
Spinning
Spinning puts in the needed twists. The slivers are wound from spool to another and while doing so the yarn is provided a twist. These yarns are much thicker as compared to cotton and silks. The yarns are sold to weavers on these spools or in skeins.
Twisting
Twisting is spinning tow, three or four yarns together. Two ply yarns are used for weaving and machine-knitting. Three and four plies are utilized for hand-knitting.
Reeling
Worsted yarns are wound around and reeled into skeins.
Inspection
Inspecting the skeins and putting them into bundles of 40 lbs, each completes worsted yarn manufacture.
Combing
Before combing the decision is made whether the fibres are to be utilized for woolen or worsted yarns and fabrics. Combing aligns longer fibres in a parallel manner so that the resulting “Worsted yarns” are smoother and stronger. The fibres are combed by passing through the combing machine. Here the fibres are laid in a very oriented arrangement.
Short fibres are removed and the remaining fibres are pulled into a twisted strand known as ‘top’. The short fibres are known as ‘noils’. Wool tops can be dyed in this form or worsted yarns can be constructed and then dyed.
Difference Between Worsted and Woolen System
- Worsteds are chosen for special uses where it is desirable to get a hard surface finish, greater durability, and sharper coloring.
- Under the worsted system, the treatment of wool from the raw state to the finished state makes it possible for the fibre to be twisted in such a manner, as to create a smoother or harder surface. This is the essential difference. Fibres can be twisted before to weaving.
- Worsted fabrics generally have smoother texture than woolens.
- Worsted takes shine more easily due to the twist.
- Worsted cloth is less bulky and lighter than woolens.
- Worsted is made up of a better grade of yarn.
- Worsted is easy to tailor and drape.
- Worsted does not easily sag and hand a crease well.
- Worsted cloth has greater tensile strength than woolens.
- Worsteds last longer than woolens.