Common Defects in Blowroom Laps
Last updated on July 19th, 2023 at 12:40 am
With the evolution of the new concept of “Zero defects”, there is growing concern in the mills to control defects at every stage of manufacture. Lap defects can in the long run result in yarn defects, thus ultimately reducing the sale value of yarn. It is in this context that an understanding of the types of lap defects, their causes and remedies assumes importance.
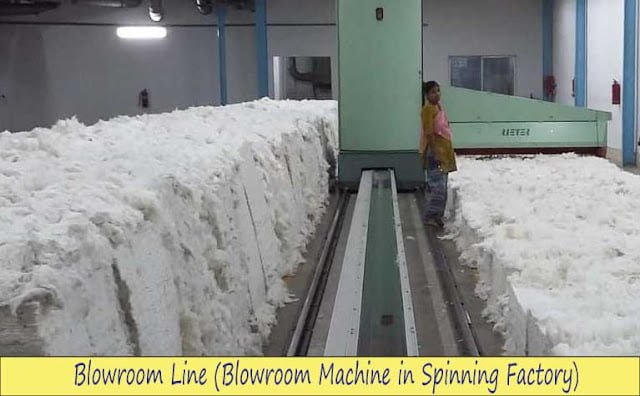
The types of lap defects commonly encountered and their likely causes are as follows:
Ragged Lap selvedges Causes
- Waste accumulation at the sides of the grid bars, cages or calender rollers, obstructing smooth flow of material.
- Torn leather linings of cages.
- Rough spot at the sides of the feed plate delivering the material to the calender rollers.
- Improper setting of selvedge guides.
Lap licking Causes
- Use of too much soft waste in the mixing.
- Too high fan speed.
- Excessive beating.
- Insufficiently weight calender rollers.
- Too much weight on lap racks.
- Either cotton is damp or departmental humidity is high.
- Sticky nature of the material and type of spin finish in the case of polyester.
Remedies
- Use of roving ends to act as layer separators.
- Incorporation of lap filters.
- Blanking off of one of the cages.
- Use of antistatic spray while processing synthetics.
- Reduction of full lap weight.
Conical laps Causes
- Improper functioning of pedals on one side to pedals being choked with dirt.
- Air entering at one side from under the grid bars of the beater.
- Defective beater blades at one side.
- Uneven suction at the cages leading to deposition of more material on one side than on the other.
- Lap spindle racks not exerting even pressure across the lap width.
Dirty laps Causes
- Blunt grid bars or grid bars not properly set i.e. set either too close or at incorrect angle.
- Grid bar interspaces choked up.
- Excessive fan speed leading to ineffective cleaning.
- Blunt and slow running beaters.
- Beater set too far from feed roller or pedals.
- Trash boxes overfull, or air current in trash box region causing retrieval of trash.
Thick and thin places in lap or patchy laps Causes
- Insufficient suction at the cages.
- Damaged cages i.e. damages wire meshing or worn-out flannel or leather linings.
- Insufficient opening of cotton lumps at the preceding machines.
- Improper removal of air from the cotton stack at the overflow box or reserve hopper feed box leading to the formation of air pockets.
Holes in lap Causes
- Damages cages.
- Too high tension draft between shell roller and calender roller.
Soft laps Causes
- Inadequate pressure at calender roller and lap rack.
- Too low tension draft between shell roller and calender roller.
- Worn out brake linings on brake pulley.
Stringiness of cotton tufts in lap Causes
- Feeding of damp cotton.
- Cotton being over-beaten either due to high beater speed, choking of beater chamber or
use too many beating points in the line. - Excessive rolling action of material in machines like the step cleaner.
Lap splitting Causes
Cotton being blown equally on both the cages.
Remedies
- Increase calender roller pressure.
- Partially blank off one of the cages.
Disturbed tufts in laps Causes
- Excessive speed of fluted lap rollers.
- Lap may be so large and bulky that it touches the plain calender rollers when it is
getting built-up. - Disturbance to tufts of the outer layer also occurs during storage and transportation.
Your very own commitment to getting the message throughout came to be rather powerful and have consistently enabled employees just like me to arrive at their desired goals.